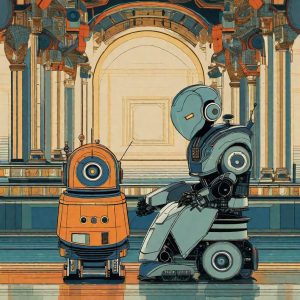
An industrial robot (IR) is a multi-purpose automatic machine with programmable control that is used to move objects in space and reproduces the driving and mental functions of a human in the performance of production processes.
This type of robotic machine has the following structure:
- A mechanical system or manipulator is a mechanism that reproduces the exact movements of human limbs (arms or legs).
- A programmable control system or computer.
- Information system.
Industrial robots have become an important and integral component of automated GMS (flexible manufacturing systems), which help to increase labor productivity. They are most commonly used in welding, painting, assembly, sampling and installation, packaging, product inspection and testing.
They are classified according to the following criteria:
- By the nature of technological operations:
- technological – perform the main operational activities in production;
- Auxiliary – their main purpose is to service the main process equipment and the transportation and storage system;
- versatile – perform a variety of tasks.
- By type of production:
- foundry;
- welding;
- forging and pressing;
- coloring;
- transportation and warehousing.
- By the coordinate system of the manipulator arm:
- rectangular;
- polar and cylindrical;
- spherical;
- angular.
- In terms of cargo:
- ultralight;
- light;
- medium;
- heavy;
- super-heavy.
- Work with electromechanical, pneumatic, hydraulic, and combined drives.
- By the type of program:
- hardwired – these robots do not have a quick program change device;
- Flexible programmable – have a device for quick program change;
- Adaptive – receive the necessary information about the environment during their work and take the necessary actions based on this data;
- intelligent – can independently plan and perform the necessary manipulations depending on the task, quality criteria, and the state of the environment.
- By the nature of the control:
- positional;
- contour;
- combined.
Technical characteristics of the PR
The technical characteristics of modern PRs can be divided into two broad groups: basic and additional.
The main ones include:
Rated load capacity is the largest indicator of the weight of an object or technological equipment in production, which guarantees their gripping, holding and movement. If the PR has many arms, the nominal load capacity is determined as the sum of the load capacity of all its limbs.
The number of degrees of mobility of the PR is the sum of possible coordinate movements of the working body relative to the support system.
The speed of movement of the manipulator links. Typically, the speed of linear movements of the working bodies of manipulators is 1.0-1.5 m/s, and the speed of angular movements is in the range of 15-360 degrees/s.
The work area is the space in which the working body of the PR is located while performing tasks. It can vary in form and scope.
The positioning or trajectory error is the deviation of the working body location from the one set by the program during its repeated repetition, which is estimated in linear or angular units.
The use of PR in production
The use of industrial robots is considered within the framework of typical industrial projects, the optimal option that meets the criteria of the task is selected, and the issues of power infrastructure, i.e. power supply, coolant supply, and integration into the production process are taken into account.
PRs most often perform the following actions:
- cable laying;
- coloring;
- assembly of electronic parts;
- Loading/unloading of technological machines and machine tools;
- Manipulating parts (e.g., stacking, sorting, transporting, and orienting);
- Moving parts and workpieces from machine to machine or from machine to pallet changer systems;
- seam welding and spot welding;
- assembly of mechanical and electrical parts;
- performing cutting operations with tool movement along a complex path, etc.
Thus, industrial robots aim to free people from performing mechanical work and reduce the risk of injuries at work.